In nearly every sector of industrial manufacturing polishing techniques are used. But often manual polishing is the only option because the tasks are too complex to be automated. Therefore in SYMPLEXITY Symbiotic Human-Robot Solutions for Complex Surface Finishing Operations will be developed.
The main SYMPLEXITY Objectives are
- Accurate and cognitive industrial robot systems enabling safe human-robot collaboration for surface finishing operations
- Easy to use interfaces for planning, control and re-planning of shared finishing tasks
- Collaboration oriented process technology for abrasive finishing, laser and fluid jet polishing
- Integrated and autonomous sensing system for objective identification of surface properties
- Introduction of developed collaborative finishing solutions into manufacturing industry.
The results of the first 4 objectives will be combined to 3 demonstrator human-robot collaboration cells, one for each of the investigated process technologies.
The 3 demonstrator cells will be tested in operational environment at 3 end-users.
SYMPLEXITY is the consistent follow-up of 3 recent EU projects that achieved TRL 4-5 (COMET - Plug-and-produce COmponents and METhods for adaptive control of industrial robots, SAPHARI - Safe and Autonomous Physical Human-Aware Robot Interaction and poliMATIC - Polishing processes and tools development.
SYMPLEXITY will bring together the results and key partners of these 3 projects to achieve TRL7 and thereby support the European Industry to win the competition in the global market with higher quality, efficient manufacturing and economic production, based on human robot collaboration for polishing complex shaped metallic surfaces.
Relevant branches are tool making, medical engineering, aeronautics and automotive industry. Case studies show, that for many applications todays >90% of manual work can be converted in 80 % of robotic work under human control and 20 % of manual work.
Web resources: |
http://www.symplexity.eu
https://cordis.europa.eu/project/id/637080 |
Start date: | 01-01-2015 |
End date: | 31-12-2018 |
Total budget - Public funding: | 8 046 375,00 Euro - 6 660 525,00 Euro |
Original description
In nearly every sector of industrial manufacturing polishing techniques are used. But often manual polishing is the only option because the tasks are too complex to be automated. Therefore in SYMPLEXITY Symbiotic Human-Robot Solutions for Complex Surface Finishing Operations will be developed. The main SYMPLEXITY Objectives areSO 1 – Accurate and cognitive industrial robot systems enabling safe human-robot collaboration for surface finishing operations
SO 2 – Easy to use interfaces for planning, control and re-planning of shared finishing tasks
SO 3 – Collaboration oriented process technology for abrasive finishing, laser and fluid jet polishing
SO 4 – Integrated and autonomous sensing system for objective identification of surface properties
SO 5 – Introduction of developed collaborative finishing solutions into manufacturing industry
In SO5 the results of the first 4 objectives will be combined to 3 demonstrator human-robot collaboration cells, one for each of the investigated process technologies. The 3 demonstrator cells will be tested in operational environment at 3 end-users.
SYMPLEXITY is the consistent continuation of 3 recent EU projects that achieved TRL 4-5:
COMET – Plug-and-produce COmponents and METhods for adaptive control of industrial robots
SAPHARI – Safe and Autonomous Physical Human-Aware Robot Interaction
poliMATIC – Polishing processes and tools development
SYMPLEXITY will bring together the results and key partners of these 3 projects to achieve TRL7 and thereby support the European Industry to win the competition in the global market with higher quality, efficient manufacturing and economic production, based on human robot collaboration for polishing complex shaped metallic surfaces. Relevant branches are tool making, medical engineering, aeronautics and automotive industry. Case studies show, that for many applications todays >90% of manual work can be converted in 80 % of robotic work under human control and 20 % of manual work.
Status
CLOSEDCall topic
FoF-06-2014Update Date
27-10-2022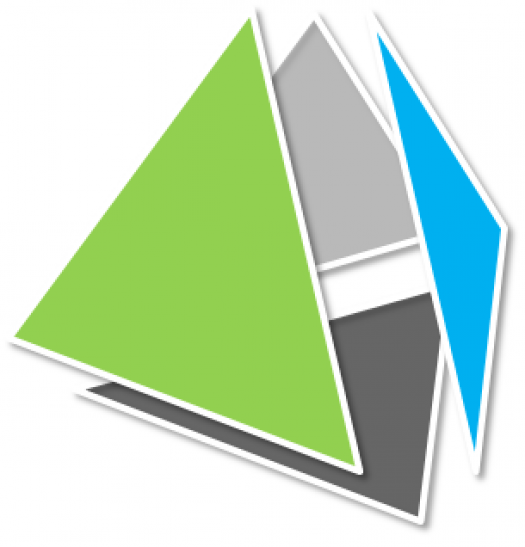