EU manufacturers are increasingly adopting automation solutions that can improve productivity and reduce costs. Enterprises’ ability to utilize these technologies may be their single most important competitive advantage, and the specific skills, experiences, competences, and flexibility of workers are pivotal to and at the core of this ability. To create a healthy workplace and increase the competitiveness of the manufacturing firms, the creation of an optimal environment for human automation integration and cooperation that harnesses and supports the workers’ capabilities is needed.
The HUMAN project, with 12 partners from 6 European countries, aims to define and demonstrate workplaces where automation and human workers operate in harmony to improve the productivity, quality, performance of the factory as well as the worker satisfaction and safety.
Objectives to be met are:
- Improving the integration of humans with their workplace.
- Enhancing the monitoring and wellbeing of human automation co-operation.
- Stimulating and advancing human-automation interaction and co-operation for optimal performance and achievement of complex tasks.
- Establishing adaptable workplaces and tasks to human cognitive and physical.
These objectives will be achieved by developing and employing physical, conceptual, methodological, technological, and knowledge-based tools. 3 use case companies from the Furniture Manufacturing (ROYO Group), Automation Manufacturing (COMAU), & Defence & Aerospace (AIRBUS) sectors are involved.
Proposed advances offered by HUMAN solutions will remove the barriers for:
- Adaptability and flexibility of humans to continuously changing workplaces.
- Alignment of new and complex tasks with human cognitive and physical skills.
- And synchronization of enterprise goals with human.
These advancements will in turn have significant impacts on higher customization capability, productivity, quality, worker satisfaction, and empower competitive position of the EU manufacturers.
Web resources: |
http://www.humanmanufacturing.eu/
https://cordis.europa.eu/project/id/723737 |
Start date: | 01-10-2016 |
End date: | 30-09-2019 |
Total budget - Public funding: | 4 533 043,00 Euro - 3 991 355,00 Euro |
Original description
EU manufacturers are increasingly adopting automation solutions that can improve productivity and reduce costs.Enterprises’ ability to utilize these technologies may be their single most important competitive advantage, and the specific skills, experiences, competences,and flexibility of workers are pivotal to and at the core of this ability.To create a healthy workplace and increase the competitiveness of the manufacturing firms, the creation of an optimal environment for human automation integration and cooperation that harnesses and supports the workers’ capabilities is needed.The HUMAN project,with 12 partners from 6 European countries, aims to define and demonstrate workplaces where automation and human workers operate in harmony to improve the productivity,quality,performance of the factory as well as the worker satisfaction and safety.Objectives to be met are:Improving the integration of humans with their workplace;Enhancing the monitoring and wellbeing of human automation co-operation;Stimulating and advancing human-automation interaction and co-operation for optimal performance and achievement of complex tasks;Establishing adaptable workplaces and tasks to human cognitive and physical skills.These objectives will be achieved by developing and employing physical, conceptual, methodological, technological, and knowledge-based tools. 3 use case companies from the Furniture Manufacturing (ROYO Group), Automation Manufacturing (COMAU), & Defence & Aerospace (AIRBUS) sectors are involved. Proposed advances offered by HUMAN solutions will remove the barriers for:adaptability and flexibility of humans to continuously changing workplaces;alignment of new and complex tasks with human cognitive and physical skills;and synchronization of enterprise goals with human expectations.These advancements will in turn have significant impacts on higher customization capability,productivity,quality,worker satisfaction,and empower competitive position of the EU manufacturers.Status
CLOSEDCall topic
FOF-04-2016Update Date
27-10-2022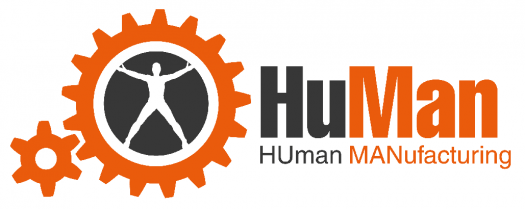